Lab 4 - PID Control
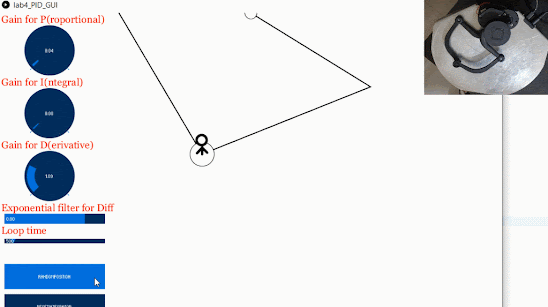
Introduction: The main objective of this lab was to gain familiarity with controlled actuation and path-following using PID control by understanding the behaviour exhibited by each parameter. Before starting any of the assessments, I noticed that precisely adjusting the PID values using the control knobs was awkward. The sketch contained code to increment these values through key presses, but these changes were not reflected on the UI. I added a few lines of code in the KeyPress() event to fix this issue, and the result made tuning the parameters much easier. Secondly, I was unable to perform any assessment with the end-effector's star-shaped "head", as the magnet on which it sits was unable to stick to my Haply. The code for this lab can be found here . 1) Run the code and try out the P controller. How does it feel? What happens when you change the target position? What does changing the P parameter do? Do you notice any problems? Snapping to the original target positio